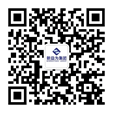
微信公眾號二維碼
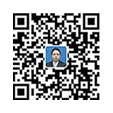
微信咨詢顧問二維碼
新益為TPM咨詢公司概述:TPM管理,英文Total Productive Maintenance的縮略語,中文譯名叫全員生產(chǎn)維護,又譯為全員生產(chǎn)保全。是以提高設備綜合效率為目標,以全系統(tǒng)的預防維修為過程,全體人員參與為基礎的設備保養(yǎng)和維修管理體系。
TPM咨詢
一、TPM管理定義
TPM管理在國內(nèi)被稱為全員生產(chǎn)維修,是生產(chǎn)現(xiàn)場設備的維護工作流程和常規(guī)的“防寒醫(yī)療技術”。目的是提高生產(chǎn)力。
TPM管理每天對工廠管理中的設備進行維護和維修,不被視為與生產(chǎn)無關。維護停機時間按計劃安排在工作日的一部分,不被視為生產(chǎn)等待現(xiàn)象。
在某些情況下,TPM管理還可以用作制造過程的一個組成部分。這樣做是為了最大限度地減少因事故和計劃外維護工作造成的損失。
二、TPM管理案例說明
一公司是一家印刷公司,主要從事包裝用瓦楞紙箱、絲網(wǎng)印刷和傳統(tǒng)的膠印業(yè)務。兩年前,公司發(fā)布了一套全自動針噴式印刷設備。它在競爭激烈的印刷市場中發(fā)揮了非常重要的作用。公司高管決定再引進幾個。
之后,公司與海外公司談判的合資企業(yè)出現(xiàn)了意想不到的問題。對方提出了很多他認為公司工廠管理層“不能接受”的問題。設備太臟,設備經(jīng)常出現(xiàn)故障,維護人員太忙,員工冷漠等等。
從合作的角度來看,投資方堅持“引進最新的TPM管理”作為一項要求,并將其包含在合同中。
起初,公司管理層覺得對方有點“多管閑事”。“有貨給你就行了,你管怎么整出來的!”公司經(jīng)理覺得這些東西太沒必要了。骯臟的設備與制造的產(chǎn)品有什么關系?
但為了順利合作,公司還是同意了。幾個月后,公司做了這些“閑事”,然后感覺煥然一新。
每天擦洗設備,減少了故障,員工也積極了。因為設備每天都要檢查,所以有些員工比維修工人更了解設備,一聽就知道了。聲音異常就知道問題出在哪里?
此次事件后,公司決定在全廠積極推廣TPM管理。
三、早期的第三次TPM
早期的TPM管理只是生產(chǎn)和設備維護部門執(zhí)行的TPM管理活動的一部分。到目前為止,很多公司和人員都專門在設備管理上進行了TPM管理活動,這實際上是目前的TPM管理模型。范圍完全擴大了,內(nèi)容也大大擴展了。自2000年以來,人們已將TPM管理的范圍擴展到供應鏈和價值鏈系統(tǒng)。這些先進的設備管理技術和精益制造業(yè)的使用,顯著減少了設備故障,提高了生產(chǎn)效率,有力地保證了精益制造業(yè)的積極發(fā)展。
如今,TPM管理推動活動在全球范圍內(nèi)傳播,效果明顯。TPM管理給企業(yè)帶來的好處體現(xiàn)在產(chǎn)品成本、質量、生產(chǎn)率、庫存周轉、安全環(huán)保、員工工作心情等方面。
四、TPM管理的內(nèi)容
TPM管理的內(nèi)容非常豐富,有3個概念、4個目標、5個理念、6個指標、8個支柱、16個大浪費、4個階段、12個步驟等等。同時本書介紹的OEE和SMED可以說是屬于TPM管理范疇的。在精益活動中,推進TPM管理是一個不可回避的環(huán)節(jié),也是非常必要的。
五、JIT要求
在低庫存和無過程異?;蛉毕莸那闆r下,JIT需要保持生產(chǎn)和設備處于良好狀態(tài)并消除6大浪費(以及最后16大浪費),需要TPM管理。沒有TPM管理,質量很差,機器經(jīng)常停機,產(chǎn)量得不到保證,JIT無法推廣。
六、成本要求
設備經(jīng)常壞,時間損失特別大。在流動性低的地方有很多浪費。制造過程不是連續(xù)的。資源通常需要冗余配置來支付意外成本。高增長是不可避免的,所以我們需要推動TPM管理。
七、文化和團隊需求
TPM管理的推廣對精益生產(chǎn)具有促進和互補作用,因為TPM管理是全員參與、獨立的管理。
你知道TPM管理的基礎知識嗎?以上就是新益為TPM咨詢公司的相關介紹,做好企業(yè)的TPM管理工作就是為精益生產(chǎn)管理活動打下基礎,讓精益生產(chǎn)管理在企業(yè)中發(fā)展有一個良好的前提。
建立生產(chǎn)有序、管理順暢,操作規(guī)范,士氣高昂、高質量、低成本、短交期的作業(yè)現(xiàn)場;
為企業(yè)規(guī)劃設計一套由內(nèi)到外的形象升級,外觀視覺價值體現(xiàn)、內(nèi)在的管理內(nèi)涵體現(xiàn);
全員參與設備管理高產(chǎn)出和低成本運營,提升設備管理能力,維護能力,提高效率
構建班組生產(chǎn)管理體系、循環(huán)評價、人才育成、持續(xù)改善、績效管理、文化養(yǎng)成體系;
提高產(chǎn)品質量、降低生產(chǎn)成本、縮短交期、增加利潤,讓管理更系統(tǒng)科學,執(zhí)行力更強
對工廠的各個組成部分進行合理安排,以提高生產(chǎn)效率、降低成本、優(yōu)化物流、改善工作環(huán)境等