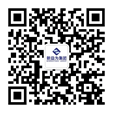
微信公眾號(hào)二維碼
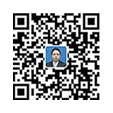
微信咨詢顧問二維碼
6S咨詢公司概述:在學(xué)習(xí)“豐田式成本管理”過程中,你是否會(huì)面臨這些疑問:比如交付模式不同、生產(chǎn)模式不同,豐田的模式是否適合于不同企業(yè)?比如在生產(chǎn)環(huán)節(jié)可以推行豐田模式,但我們工程項(xiàng)目性交付越來越多,豐田的生產(chǎn)成本管理方法能否適用?
作業(yè)成本管理
問:能化企業(yè):我們的生產(chǎn)模式、交付模式與豐田不同,小批量多品種,豐田的成本管理方法能否適用?
答:適用。從業(yè)界不同的企業(yè)來看,許多與豐田差異很大但追求卓越的企業(yè)都在學(xué)習(xí)豐田的成本管理思想。
【案例】華為公司現(xiàn)在已是世界第二大通信設(shè)備供應(yīng)商,服務(wù)全球三分之一的人口,作為通訊的高新技術(shù)企業(yè)和豐田這樣的傳統(tǒng)制造企業(yè)差異很大。華為生產(chǎn)體系于2004年底成立項(xiàng)目組,后聘請(qǐng)豐田生產(chǎn)方式創(chuàng)始人大野耐一創(chuàng)辦的咨詢公司做顧問,進(jìn)行生產(chǎn)現(xiàn)場(chǎng)精益改善活動(dòng)。
改善的效果是顯著的,從2006年到2008年制造周期3年縮短了79.1%,體現(xiàn)生產(chǎn)效率的標(biāo)準(zhǔn)工時(shí)降低率自06年起每年比上一年度平均提升15%,萬元發(fā)貨制造費(fèi)用07年比06年下降8.8%,萬元發(fā)貨料本制造費(fèi)用08年比07年下降6.4%。這個(gè)案例說明生產(chǎn)模式不同,并不妨礙豐田精益思想在企業(yè)供應(yīng)鏈中的應(yīng)用與推廣。
【應(yīng)用】能化企業(yè)生產(chǎn)模式多為小批量、多品種,個(gè)性化較高,生產(chǎn)過程中等待多、浪費(fèi)多,在制造環(huán)節(jié)不宜形成規(guī)模經(jīng)濟(jì)。而市場(chǎng)的激烈競(jìng)爭(zhēng)對(duì)價(jià)格、快速供貨的要求越來越高,在這種情況下,不斷加強(qiáng)供應(yīng)鏈的快速響應(yīng)能力、降本增效就成了當(dāng)務(wù)之急。
因此,生產(chǎn)體系選擇以縮短制造周期、節(jié)約成本為主線持續(xù)進(jìn)行成本改善,持續(xù)減少和消除各種等待和浪費(fèi)是非常必要的。越改善,可改善的空間越大,通過豐田提供的工具和方法查找問題,原來看來不是問題的,也變成需要消除的浪費(fèi),就有了再找問題進(jìn)行改善的動(dòng)力。
總結(jié):豐田成本管理思想有助于提升企業(yè)供應(yīng)鏈的競(jìng)爭(zhēng)優(yōu)勢(shì),并不受生產(chǎn)模式的影響。
問:在生產(chǎn)環(huán)節(jié)可以推行豐田模式,但我們工程項(xiàng)目性交付越來越多,豐田的生產(chǎn)成本管理方法能否適用?
答:產(chǎn)生這種疑問源自對(duì)豐田的誤讀,提起豐田的精益生產(chǎn),往往被狹隘地理解為僅適用于“生產(chǎn)”環(huán)節(jié),實(shí)際上精益思想早就發(fā)展為以整個(gè)企業(yè)為中心的“精益企業(yè)”的觀念。在豐田汽車看來,精益模式是一種不斷改進(jìn)、強(qiáng)調(diào)持續(xù)創(chuàng)新的企業(yè)精神,這種精神早已滲透到豐田的各個(gè)層面,而不僅是生產(chǎn)層面。
【案例】華為的工程項(xiàng)目交付比重非常大,但華為的工程項(xiàng)目交付大量融合了豐田的精益管理理念。華為工程項(xiàng)目管理是如何通過豐田理念將工程項(xiàng)目管理落地的?
移動(dòng)通信工程項(xiàng)目具有傳統(tǒng)土木工程項(xiàng)目固定性、一次性、單件性的特征,總得來說就是客戶個(gè)性化需求較高,與能化企業(yè)工程項(xiàng)目具有相似性。為了保證項(xiàng)目交付質(zhì)量、持續(xù)降成本的需求,豐田的標(biāo)準(zhǔn)作業(yè)、原單位管理扮演著至關(guān)重要的角色,并有效支撐了前期報(bào)價(jià)、提高了項(xiàng)目預(yù)算準(zhǔn)確度,及項(xiàng)目過程管理。
i. 作業(yè)標(biāo)準(zhǔn)化
華為工程項(xiàng)目管理引入豐田工序、工藝、工時(shí)、工具標(biāo)準(zhǔn)化的理念,輸出作業(yè)指導(dǎo)書,形成作業(yè)標(biāo)準(zhǔn)化,在工程項(xiàng)目全過程推行,有效縮短了安裝驗(yàn)收周期,支撐公司全流程存貨周轉(zhuǎn)的改善,提高安裝效率,降低綜合交付成本。
ii. 建立原單位、基線管理機(jī)制
首先將項(xiàng)目拆分至工序,并且制定每道工序下物料、工時(shí)、工具、設(shè)備使用量,進(jìn)一步將工序分解為若干標(biāo)準(zhǔn)子工序,結(jié)合BOQ(工程量清單,Build of Quantity),確定每道子工序人、材、機(jī)消耗量,套用當(dāng)?shù)厥袌?chǎng)人、材、機(jī)單價(jià),計(jì)算出具體站點(diǎn)(最小安裝單元)模型的工程成本,使站點(diǎn)建設(shè)成本和利潤(rùn)透明化。
一方面在給客戶報(bào)價(jià)的時(shí)候,能夠準(zhǔn)確計(jì)算此項(xiàng)目的利潤(rùn)與成本。另外一方面,對(duì)于分包商“高估冒算”項(xiàng)目和超額利潤(rùn)率得以暴露,分包價(jià)格得以降低,一舉兩得。這個(gè)案例說明,豐田標(biāo)準(zhǔn)化工序、原單位管理是進(jìn)行工程項(xiàng)目成本管理的基礎(chǔ)。
總結(jié):豐田成本管理思想有助于提升工程項(xiàng)目交付的競(jìng)爭(zhēng)優(yōu)勢(shì),可應(yīng)用于工程項(xiàng)目中。
建立生產(chǎn)有序、管理順暢,操作規(guī)范,士氣高昂、高質(zhì)量、低成本、短交期的作業(yè)現(xiàn)場(chǎng);
為企業(yè)規(guī)劃設(shè)計(jì)一套由內(nèi)到外的形象升級(jí),外觀視覺價(jià)值體現(xiàn)、內(nèi)在的管理內(nèi)涵體現(xiàn);
全員參與設(shè)備管理高產(chǎn)出和低成本運(yùn)營(yíng),提升設(shè)備管理能力,維護(hù)能力,提高效率
構(gòu)建班組生產(chǎn)管理體系、循環(huán)評(píng)價(jià)、人才育成、持續(xù)改善、績(jī)效管理、文化養(yǎng)成體系;
提高產(chǎn)品質(zhì)量、降低生產(chǎn)成本、縮短交期、增加利潤(rùn),讓管理更系統(tǒng)科學(xué),執(zhí)行力更強(qiáng)
對(duì)工廠的各個(gè)組成部分進(jìn)行合理安排,以提高生產(chǎn)效率、降低成本、優(yōu)化物流、改善工作環(huán)境等